Standardised Kit of Parts
Kit of parts construction, or a “platform” approach, attempts to achieve flexibility in assembly and efficiency in manufacture. It is a collection of engineered parts that can fit together for a variety of configurations to create a family of related objects that all work with each other. This approach can be used in manufacturing, industrial design, architecture, and a variety of other fields. It relies upon the use of standardised systems for engineering and fabricating components, to create objects that can be easily constructed, deconstructed, extended, and reconfigured to meet changing needs.
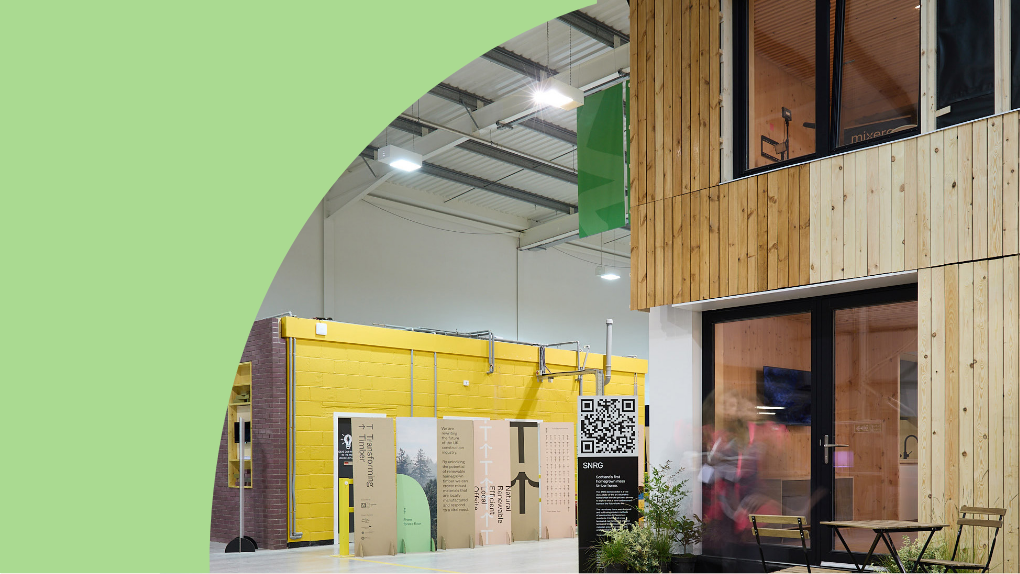
The term Mass Timber can be described as the family of Solid Laminate Timber Systems (SLTS) produced by connecting a series of smaller timber elements together to form larger panel or beam products. Various forms of Solid Laminate Timber Systems (Figure 1) are available today. These include systems that are glued, such as Cross Laminated Timber (CLT / CrossLam / X-Lam), Glue Laminated Timber (GLT or Glulam), Laminated Veneer Lumber (LVL), and those that are non-glued, such as Nail Laminated Timber (NLT / Nail-Lam) as well as others that use moisture movement for connectivity such as Dowel Laminated Timber (Brettstapel / Dowel-Lam / DLT) and interlocking Cross Laminated Timber (ICLT).
The project team developed a new mass timber product called a Glue Laminated Timber Portal (GLTP) frame. A GLTP functions under the same principles as a steel portal frame where it acts as a load bearing component. Due to its complicated shape, clamps are used, instead of the vacuum press, to allow the glue to cure. One additional advantage of this system is the rotational stiffness or moment transferring properties. This has been utilised to withstand wind loading on perpendicular building faces.
Principle Outputs
Family of standardised kit of parts developed using homegrown timber
Benefit of new mass timber product called Glue Laminated Timber Portal (GLTP) frame
NLT components developed and tested using timber beech nails
Structural digital design tool created within the project will carry out the design checks required for building applications for GLTP, NLT and CLT
Conclusion
P-DfMA has already made inroads into construction, where sets of components or assemblies are mass produced to be put together in a multitude of ways and across multiple building types. The Transforming Timber project, through its “Living Labs”, evidenced how a single component can be used as part of a house, a school, a commercial development, a holiday cabin or an extension.
-
Supported by
-
Project Partners
-
-
-