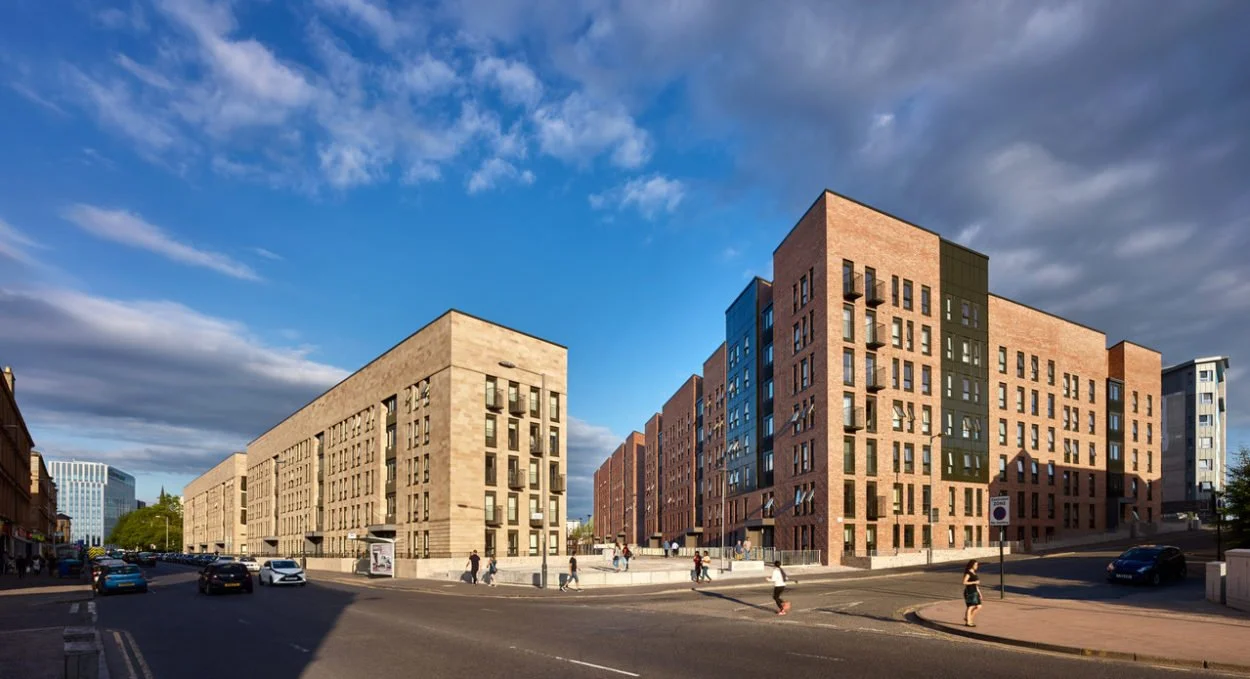
Client: Sanctuary Scotland Housing Association
Contractor: CCG
Timber frame contractor: CCG OSM
Phase 4&5 Architect: Collective Architecture
Anderston Regeneration
City regeneration breathes new life into central urban living
The Anderston Regeneration is a five-phase multi-award winning project that has changed the face of a key urban quarter in Glasgow city centre. More than a decade in the making, the project involved replacing damp, highly inefficient 1960s-built concrete flats with a modern interpretation of the Victorian tenement-style housing that once stood in the area.
The new homes are a mix of 2-storey townhouses and 4, 5, 6 and 7-storey flats, constructed using a closed panel timber system together with traditional blockwork and clad in a selection of complementary materials and colours that reflect the area’s history.
Completed in 2011, phases 1 and 2 brought a total of 176 flats that were a fresh take on the housing of the area with a mix of traditional brickwork and multi-coloured aluminium panels – one block in Phase 2 even has a homage to the famous Scottish comedian, Billy Connelly.
Phase 3A and 3B, 49 mixed-tenure homes and 109 flats respectively, were constructed over a two-year period, each again reflecting the historical tone of the Anderston area and this time clad using a mix of buff brick and zinc panelling.
Meanwhile, the final 206 properties constructed in phases 4 and 5 were clad in a mix of sandstone and buff brick, highlighted with powder-coated alumnium.
The Anderston Regeneration Masterplan was designed to re-house the existing Anderston community. With such an extensive re-housing initiative, the homes had to be constructed faster and to a far greater environmental standard to combat the issue of fuel poverty.
Taking a fabric-first approach, the chosen method of construction was timber frame. CCG OSM’s enhanced closed panel ‘iQ’ system, together with traditional blockwork for the taller blocks, was used across all phases.
The ‘iQ’ timber frame system was constructed offsite by CCG with insulation, internal wall linings, windows and doors all pre-installed before being transported to site, resulting in considerable time-savings in the construction timeline.
In addition to the timber frame, all internal, flat entrance and common stairwell timber door sets were designed and manufactured by CCG Manufacturing.
Through the use of this timber system, energy-saving appliances and solar PV, residents can expect long-term energy savings thanks to a more efficient use of energy and a reduction in heat loss.